faigle wheels for TGW Logistics
TGW Logistics Group is a leading global supplier of intralogistics solutions for the fashion and textiles, food, e-commerce and general retail sectors. The Austrian specialist has been providing highly automated facilities for its international customers – from Adidas to Zalando – for 50 years. As a systems integration specialist, TGW takes responsibility for planning, system production and installation at complex logistics centres, handling everything from mechatronics and robotics to control systems and software.
For TGW, it is vital to operate as an industry pioneer in order to achieve success in this highly competitive market. This is where faigle Kunststoffe comes into play: this Austrian family business develops and manufactures components and assemblies made from engineering plastics – in particular wheels, as well as components subject to dynamic stress – for intralogistics systems. TGW brought the plastics specialist on board as a development partner with a view to enhancing the efficiency of the Stingray shuttle.
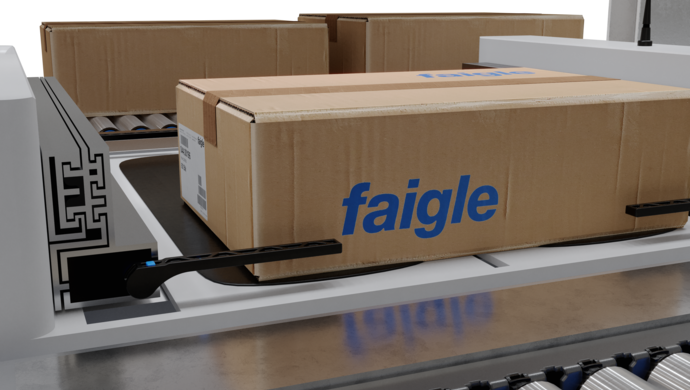
A familiar intralogistics challenge
More specifically, the focus was on further improving the shuttle’s performance, speed and dynamics – in other words, its overall efficiency – when storing and picking goods. TGW used wheels with a metal hub with a cast polyurethane (PU) tire. Due to the metal hub, such wheels are very stiff, meaning they cannot effectively dampen vibrations. These unwanted oscillations can result in stored packages shifting out of position or tilting, which in turn means that they can longer be picked up by the shuttle’s telescopic arms.
In such cases, the shuttle level concerned must be shut down under certain circumstances and the goods retrieved by hand – stoppages like this are expensive and a nightmare scenario for high-performance logistics centres.
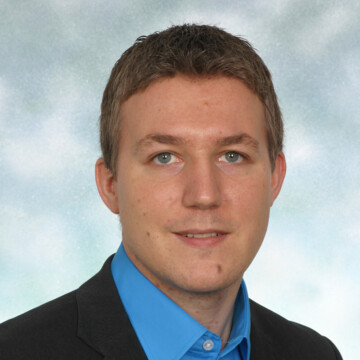
Johannes Schauer
CHIEF DEVELOPER MECHATRONICAL PRODUCTS AT TGW
Full-line perspective
Taking into account the requirements for the various components, faigle worked with TGW to draw up a concept that highlighted potential improvements. In development processes like this, the emphasis is always on the entire application – both the shuttle in operation and as part of the overall system. For instance, the loads to which individual components are exposed, the ambient temperature in which they operate, their service life and other factors are all examined. But maximising plant availability is always the overriding focus of the analysis.
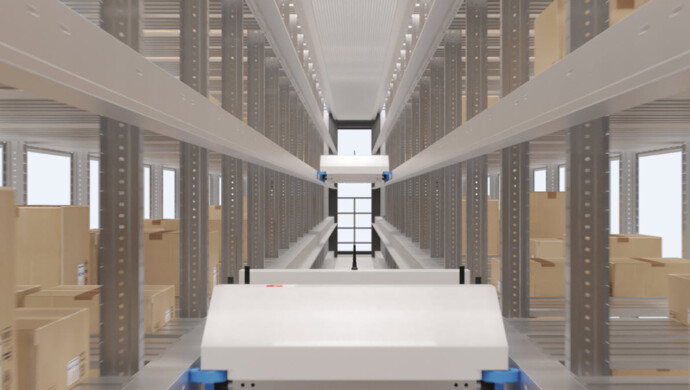
Less metal helps to reduce weight
Based on the results of the analysis, the plastics experts identified two starting points from which they could further enhance the TGW shuttle’s efficiency. faigle developed special shuttle wheels as well as new shuttle flaps, both made from plastic.
Plastic shuttle flap for weight reduction
One of the measures designed to reduce the module’s weight was replacing the conventional metal shuttle flaps – these milled steel parts are extremely complex to produce. They were re placed by a flap specially developed by faigle: an injection moulded part made from high performance plastic.
“This component is a great example of faigle’s plastics expertise, because such a complex layout and production really demand a light touch and experience,” explains Johannes Schauer, Chief Developer Mechatronical Products at TGW.
faigle’s plastics specialists used state-of-the-art simulation tools to calculate the component’s complex geometry, including anisotropic fibre orientation. The new part reduced the weight of the flaps by 80% (or 150g per flap); it is also electroconductive. Although it is extremely light thanks to the material used, the flap is highly resilient with outstanding durability. Injection moulding also helps to reduce manufacturing costs and shorten delivery times. During the various phases of the shuttle redevelopment, faigle provided TGW with a range of sample wheels and flaps for testing and evaluation. This was followed by extensive testing by both companies. For instance, TGW subjected the new plastic flap to tests equivalent to five million load cycles be- fore it entered regular operation with customers.
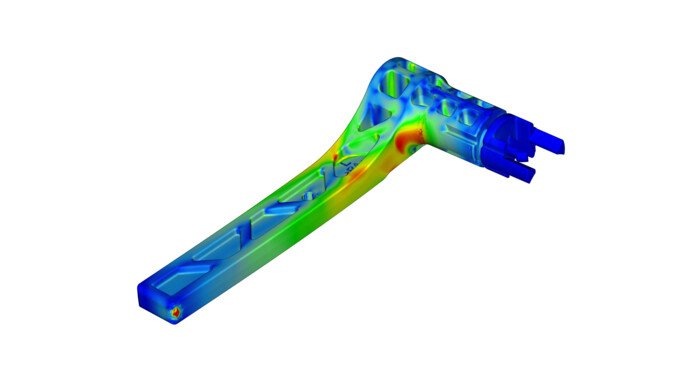
Long-lasting plastic shuttle wheels
faigle also achieved outstanding results with its newly developed shuttle wheels. The original cast polyurethane wheels were replaced with significantly lighter plastic ones. faigle used injection moulding to produce these innovative components. Alongside their weight, the wheels’ reliability is another key advantage. Production now only takes seconds, so faigle can manufacture rollers more cheaply. TGW has benefited from increased cost effectiveness in procurement, as well as from enhanced availability during demand peaks.
Heavy-duty and vibration dampening
When developing the new wheels, the main challenge was to avoid strong vibrations in the system, as these are transferred to the entire high rack via the shuttle track. In fact, the new wheels helped to reduce vibrations at the facility – the plastic wheels are less stiff, so they dampen vibrations more effectively than metal. faigle also carries out finishing work on the roller surface in order to further optimise the concentricity of the wheels. And the high-performance plastics used for the running surface make a substantial contribution to increased efficiency. The shuttle tires are made from the specially developed material PAS-PU and stand out for their exceptional resilience – as a result, the rollers hardly flatten, even after longer stoppages, and the starting resistance is minimised.
This vital factor also has a positive impact on energy consumption. The tires are hydrolysis-resistant, abrasion-proof and tear-resistant. Various tests and over 20 years of operation in practice have shown that their application, especially in humid environments, can more than double the service life of running surfaces in comparison with conventional materials.
Now that vibrations have been cut, packages can no longer shift and the shuttles can transport even the most sensitive products without any problems. The new wheels have also made theentire system quieter, which has been particularly well received by the workers at the logistics centre.
Contact us
If you have any questions or need further information, we’ll be happy to talk to you.
Contact usMichael Schrom
LEITER RESEARCH & DEVELOPMENT VON FAIGLE KUNSTSTOFFE
Outstanding development results
“This joint process has delivered substantial efficiency gains, enhanced reliability and extended shuttle lifespans. And first and foremost, this benefits our customers,” emphasises Johannes Schauer, Chief Developer Mechatronical Products at TGW.
The development partnership between the two companies stretches back more than 30 years.
Innovation workshops aimed at optimising developments
“Many plant engineering companies turn to us because they want to reduce the weight of their devices or boost energy efficiency. Thanks to our plastics know-how, we can act as a sparring partner and make a significant contribution to the optimisation process. Our experience enables manufacturers to replace various metal components with lightweight, efficient and competitively priced injection-moulded parts,” points out Michael Schrom, head of research and development at faigle Kunststoffe.
The plastics specialist stages innovation workshops where in-house experts work with customers’ technicians to draw up bespoke solutions – all the way from the initial idea through to production readiness. The participants also receive insights into a range of materials, processing methods and plastics properties, as well as solutions implemented in other industries. Every year, faigle delivers 25 million rollers to big-name manufacturers for applications such as warehouse logistics systems, and sorting and conveying systems.
TGW products
Shuttle flaps
How can I help you?
Hi, I’m Jennifer Wachter. I’d be happy to talk to you about our products and answer any questions you might have on our custom solutions.
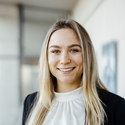
If you have any questions or need further information, we’ll be happy to talk to you.
Additional information
Development