01.
02.
03.
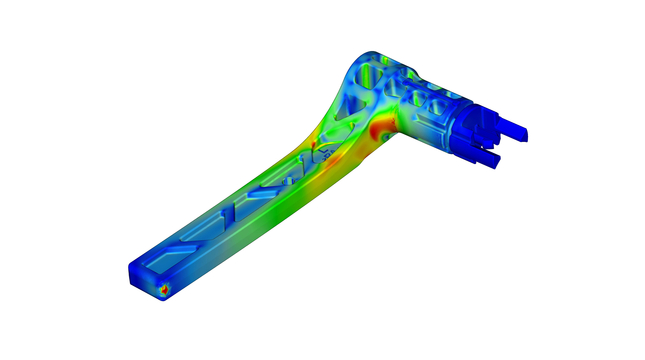
Material flow and warehouse logistics solutions for warehousing, production, order picking and distribution need to become more efficient in terms of performance, speed and dynamics, if they are to keep up with increasingly rigorous requirements. Particularly when it comes to storing and picking goods, unwanted vibrations must be avoided so that stored packages do not shift out of position or tilt, which means that they can no longer be picked up by a shuttle’s grippers. In such cases, the shuttle level concerned must be shut down under certain circumstances and the goods retrieved by hand – stoppages like this are expensive and a nightmare scenario for high-performance logistics centres.
Shuttle wheels have a metal hub, which makes them very stiff and means they are unable to dampen vibrations effectively. So faigle set about producing special shuttle wheels as well as new shuttle flaps, both made from plastic . The aim was to overcome the problem of vibrations, while also reducing the weight of the parts. faigle’s plastics specialists worked closely with TGW and used state-of-the-art simulation tools to calculate the components’ complex geometry, including anisotropic fibre orientation. During the various phases of the shuttle redevelopment, faigle provided TGW with a range of sample wheels and flaps for testing and evaluation.
The new flap is 80% lighter (a reduction of 150g per flap); it is also electroconductive. Although it is extremely light thanks to the material used, the flap is highly resilient with outstanding durability. Injection moulding also helps to cut manufacturing costs and delivery times. Now that vibrations have been reduced, packages can no longer shift and the shuttles can transport even the most sensitive products without any problems. The new wheels have also made the entire system quieter, which has been particularly well received by the workers at the logistics centres.
Shuttle flaps and shuttle wheels
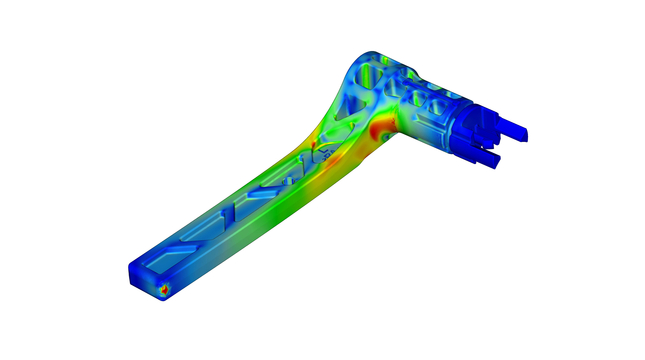
Material flow and warehouse logistics solutions for warehousing, production, order picking and distribution need to become more efficient in terms of performance, speed and dynamics, if they are to keep up with increasingly rigorous requirements. Particularly when it comes to storing and picking goods, unwanted vibrations must be avoided so that stored packages do not shift out of position or tilt, which means that they can no longer be picked up by a shuttle’s grippers. In such cases, the shuttle level concerned must be shut down under certain circumstances and the goods retrieved by hand – stoppages like this are expensive and a nightmare scenario for high-performance logistics centres.
Shuttle wheels have a metal hub, which makes them very stiff and means they are unable to dampen vibrations effectively. So faigle set about producing special shuttle wheels as well as new shuttle flaps, both made from plastic . The aim was to overcome the problem of vibrations, while also reducing the weight of the parts. faigle’s plastics specialists worked closely with TGW and used state-of-the-art simulation tools to calculate the components’ complex geometry, including anisotropic fibre orientation. During the various phases of the shuttle redevelopment, faigle provided TGW with a range of sample wheels and flaps for testing and evaluation.
03.
Products
The new flap is 80% lighter (a reduction of 150g per flap); it is also electroconductive. Although it is extremely light thanks to the material used, the flap is highly resilient with outstanding durability. Injection moulding also helps to cut manufacturing costs and delivery times. Now that vibrations have been reduced, packages can no longer shift and the shuttles can transport even the most sensitive products without any problems. The new wheels have also made the entire system quieter, which has been particularly well received by the workers at the logistics centres.