01.
02.
03.
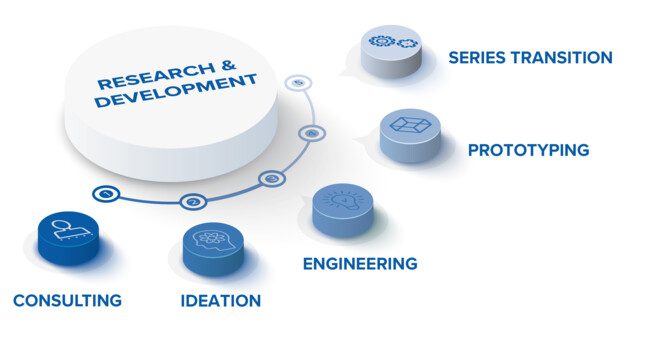
- Consulting on applications engineering
- Selecting plastics materials
- Presenting practical use cases
- Jointly identifying customer needs and operating conditions
- Developing concepts and product ideas
- Implementation and technical feasibility checks
- Implementation and economic feasibility checks
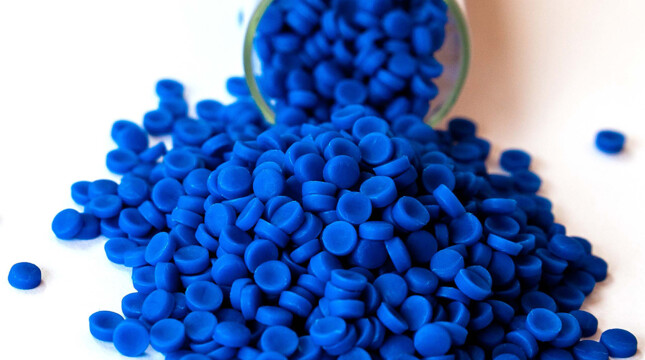
- Developing new, custom materials
- Implementing detail engineering
- Calculating specifications
- Performing simulations
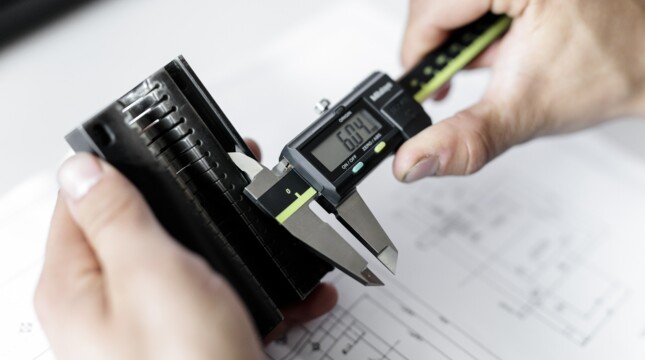
- Separate in-house R&D department with team of experts
- Technology and process refinement
- Own injection moulding plant
- 3D printing
- Product realisation
- Project and process management
- Quality management
How we approach custom development projects
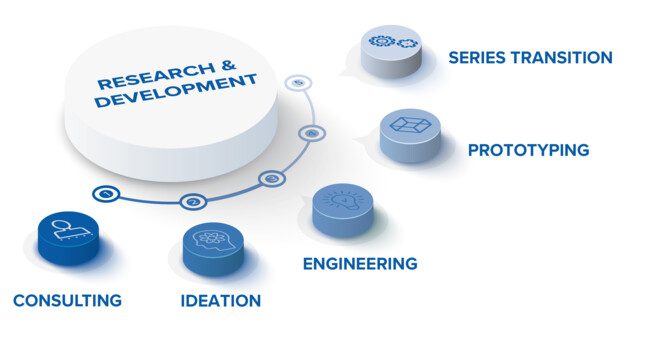
Consulting
- Consulting on applications engineering
- Selecting plastics materials
- Presenting practical use cases
Ideation
- Jointly identifying customer needs and operating conditions
- Developing concepts and product ideas
- Implementation and technical feasibility checks
- Implementation and economic feasibility checks
02.
Engineering
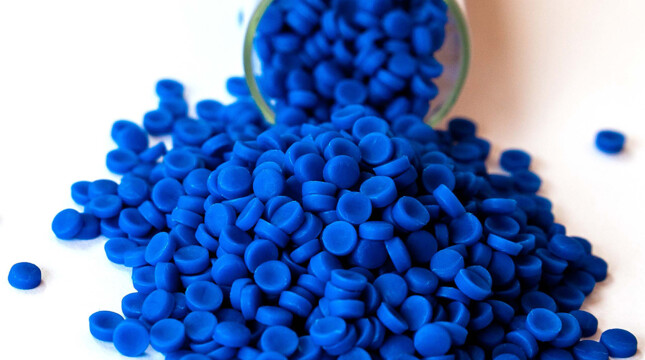
Engineering
- Developing new, custom materials
- Implementing detail engineering
- Calculating specifications
- Performing simulations
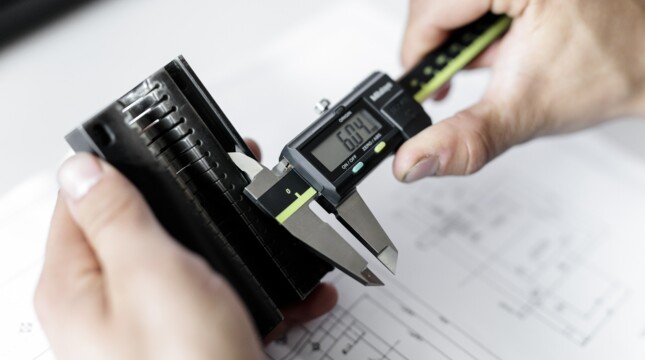
Prototype construction and test samples
- Separate in-house R&D department with team of experts
- Technology and process refinement
- Own injection moulding plant
- 3D printing
Efficient transition to volume production
- Product realisation
- Project and process management
- Quality management
Do you have any special requirements?
We serve as a development partner for customers, suppliers, partners and research facilities around the world.
Contact usSpecialist industry expertise
The combination of all-round expertise in plastics applications and industry experience is one of faigle’s core competences. And our development centres in Europe and Asia mean we are close to our customers around the globe. For decades, faigle has been a development partner to a wide range of OEMs.
Our teams of experts use filling simulation programs and rapid prototyping to help the customer get a feel for the product early on the development phase. In turn, this enables customers to become familiar with the product, and test its properties and behaviour in the early stages of the product development process. This ensures a smooth transition to volume manufacturing once the item enters production.
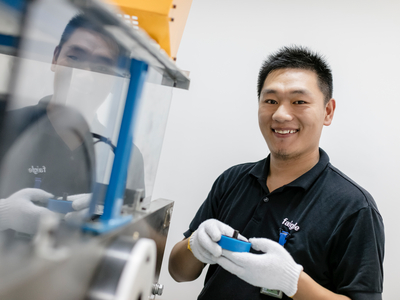
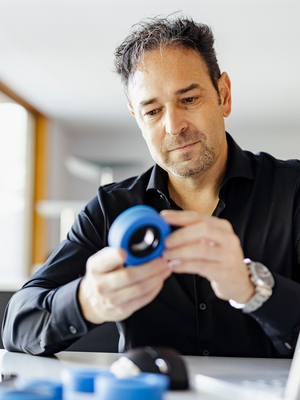
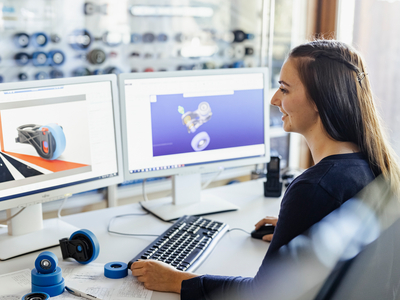
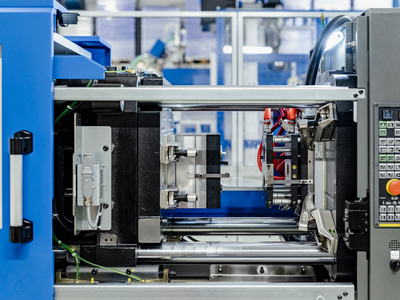
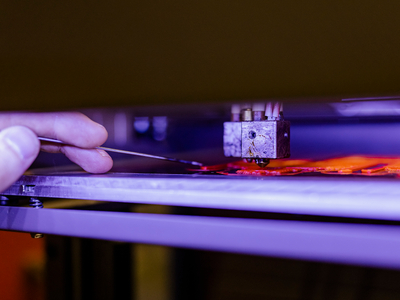

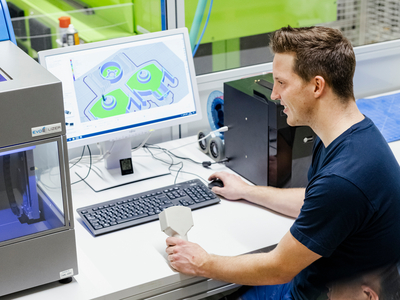

Case Study: Optimising an intralogistics shuttle for TGW Logistics Group
FAIGLE WHEELS FOR TGW LOGISTICS
As a systems integration specialist, TGW takes responsibility for planning, system production and installation at complex logistics centres, handling everything from mechatronics and robotics to control systems and software.
For TGW, it is vital to operate as an industry pioneer in order to achieve success in this highly competitive market. This is where faigle Kunststoffe comes into play: this Austrian family business develops and manufactures components and assemblies made from engineering plastics – in particular wheels, as well as components subject to dynamic stress – for intralogistics systems. TGW brought the plastics specialist on board as a development partner with a view to enhancing the efficiency of the Stingray shuttle.
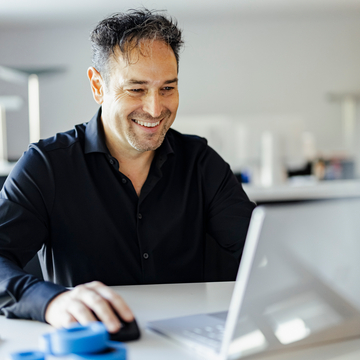
Michael Schrom
HEAD OF R&D
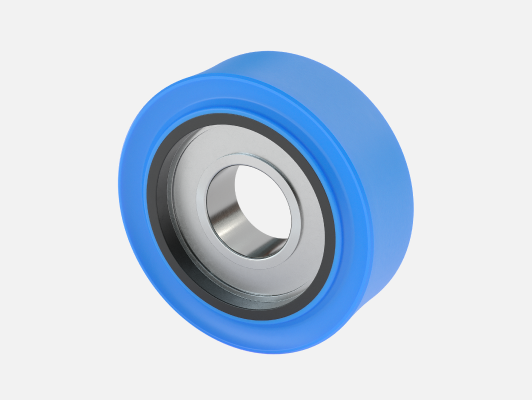
faigle and Kardex team up to optimise wheels for vertical storage system
CASE STUDY: 2K WHEEL FOR KARDEX
Thanks to a combination of innovative spirit and close collaboration, Kardex and the faigle Group have jointly developed a new guiding wheel for the Vertical Lift Module (VLM) storage system. Made from high-performance plastics, the new wheel’s lightweight construction gives it a clear edge over its predecessor. And this small part can also effortlessly withstand the huge forces it is exposed to at high operating speeds. Another advantage of this faigle innovation: production using injection moulding delivers clear benefits when it comes to cost effectiveness.
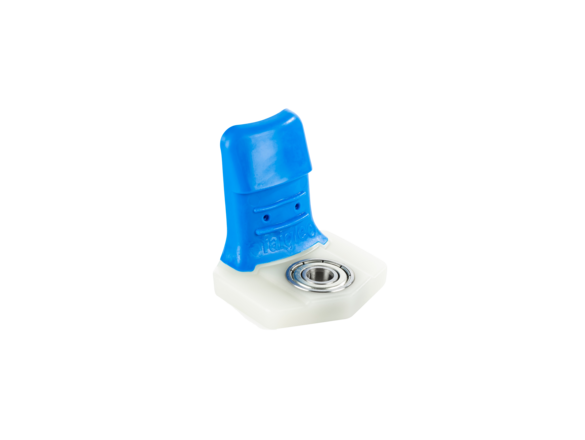
Bespoke customer solutions for latex dipping lines
Both are highly sensitive materials with a thickness of just 0.1mm. Latex and nitrile rubber gloves are often used where hygiene is vital, so when it comes to manufacturing, the emphasis is on ensuring clean, zero-error production.
High quality standards
faigle’s high-performance plastic parts more than live up to these exacting safety requirements. Maximum quality and excellent durability are absolutely essential, whatever the production volume. In Malaysia alone, the country’s disposable glove industry uses millions of components produced by faigle. So we play an important part in helping to meet worldwide demand for protective gloves.
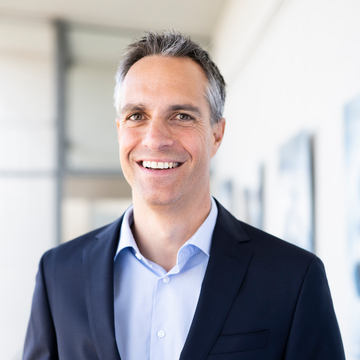
Pavel Domes
SALES DIRECTOR
How can I help you?
Hi, I’m Clemens Vögel. I’d be happy to talk to you about our products and answer any questions you might have on our custom solutions.
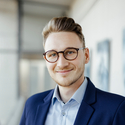
Send e-mail
Want to find out more about us?
Materials
Quality Management